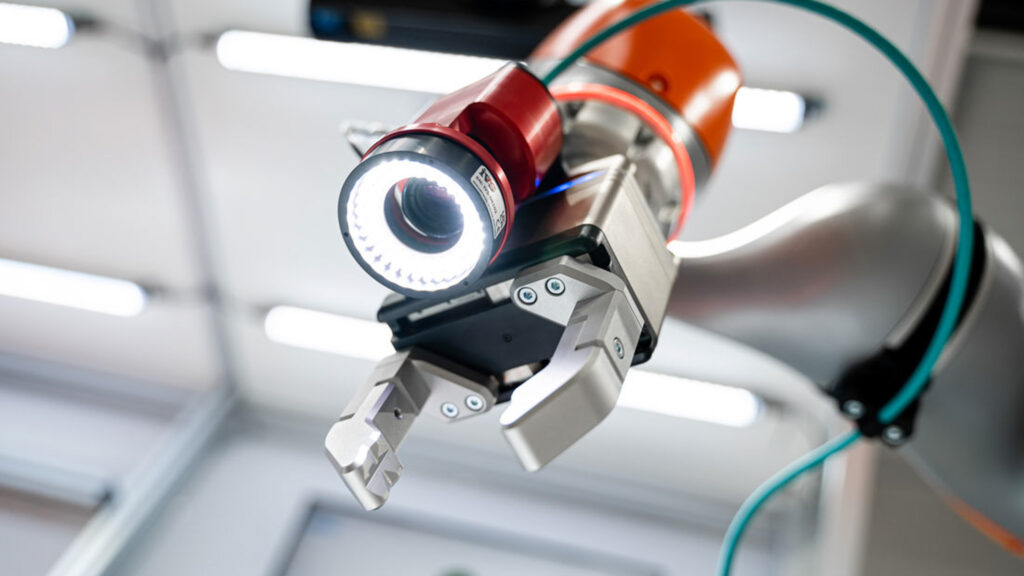
Non-destructive testing robot for the Aerospatial Industry
Non-destructive testing robot for the Aerospatial Industry
Robotic solution for non-destructive testing of large composite partsAs part of a research and development project funded by the Walloon Region, Cilyx has developed and built a non-destructive control cell for the detection of defects during the manufacture of composite parts. Designed for the constraints of the aviation industry, this cell integrates several inspection technologies and allows the complete automation of the scan of large parts with complex geometry. Two inspection methods are used: shearography and thermography. The programming of inspection trajectories is carried out offline based on the CAD modeling of the components to be inspected.
Benefits
Here are the advantages of using this robot:
- Multi-method inspection: the cell integrates several different NDT control technologies
- Fully automatic execution of scan sequences
- Saves time and repeatability compared to manual inspection
- Programming based on CAD models of parts to be inspected
- Ease of use
- Ability to inspect large parts and complex geometry
- Modular system for future integration of other equipment
Technical specifications
Elements | Processing range |
---|---|
Caractéristiques |
|
Collaboration
Interested by the subject ? You want to discuss it further with an expert ?
Take contact with our experts and received personalised advices.
Discover our associated solutions available at Cilyx :
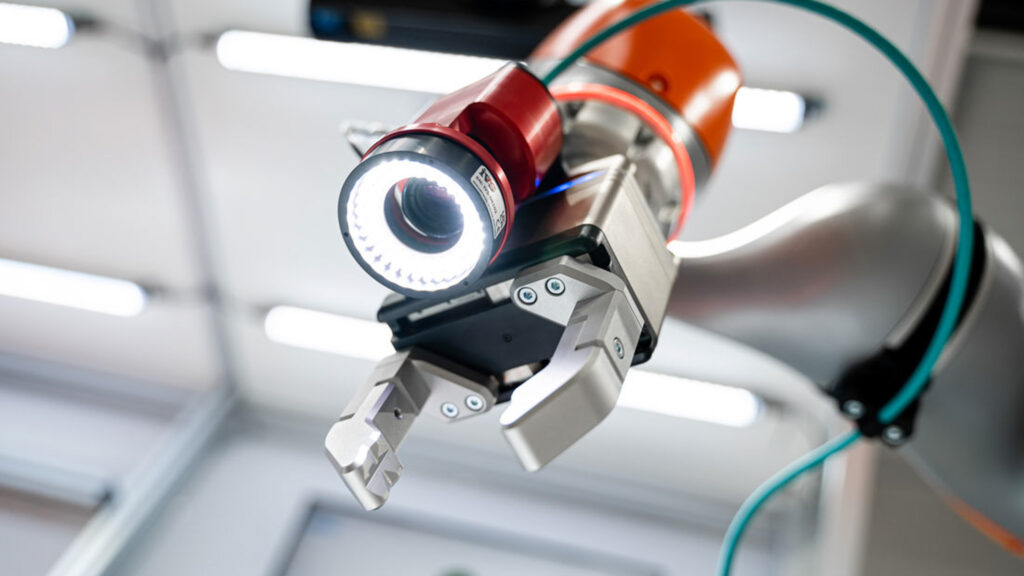
Automated quality control refers to the use of technology, such as computers or robots, to monitor and maintain the quality of products or processes.
More info